EQUIPMENT EMBEDDED IN THE CUSTOMER PRODUCT
INSTRUMENTED TBM CUTTING WHEEL
In order to measure the wear of the Tunnel Boring Machine wheels, the EFS design office has developed an embedded, autonomous, and wireless device.
Cette solution permet une installation non visible, molette montée, avec une transmission des données par radio.
- On-board equipment in the customer’s wheel
- Solution without connection and not visible when the wheel is mounted
- Autonomous and wireless on-board equipment
IN THE BEGINNING
A TBM manufacturer wants to instrument its cutting wheels to predict their replacement
CONTEXT
The roller’s environment is highly constrained: high vibration, temperature at 100°C, major shocks from falling rocks, etc.
SOLUTION
On-board equipment in the cutting wheel: no connection required for ease of use.
ON-BOARD EQUIPMENT IN THE WHEEL
Customer problem
A TBM manufacturer asked us to provide a solution for measuring wear on a cutting wheel head.
- The wheel had to be able to be dismantled by anyone (no knowledge of electronics required, but rather someone used to work on construction sites).
- Harsh environment: gravel and pebbles falling continuously onto the wheel, pressurized hot water jet with detergents, operating temperature of up to 100°C.
- As a result of the pressure exerted on the rock to shred it, the vibration of the part is significant and permanent.
EFS response
These constraints have been incorporated into our solution, enabling us to provide a response that is perfectly tailored to your needs:
-
- Equipment embedded in the wheel (resinated and placed under the metal parts)
- 3 solutions developed to avoid any electrical connection:
– Data transmission by radio, even in the event of partial immersion
– Battery life adapted to the mechanical life of the wheel
– Non-contact identification of the cutting wheel for the tracking on the cutting head.
Advantages of the on-board equipment solution
- The solution deployed was radio transmission because it simplified the wiring in the scroll wheel and in the TBM.
- This integration made it possible to know more precisely the environment in which these knobs are used and to intervene on them only when necessary. The ROI is quickly validated due to the cost of immobilizing the TBM.
- The entire solution is returned to the driver via a CAN field network available on the TBM.
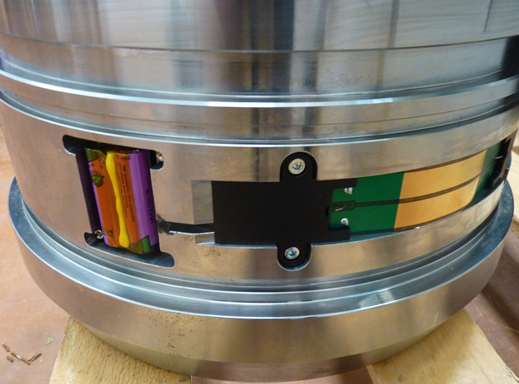
See our brochure
INSTRUMENTATION
Send download link to: