SINGLE OR MULTI-CHANNEL INJECTOR PRODUCTION TEST BENCH
Gasoline, Diesel, or Ethanol Injector Production Test Bench
The injector production test benches enable automated test cycles to be reproduced for each type of injector to be produced.
During this cycle, all the measurements qualifyiing the injector and integrated into the test are recorded at each turn.
Then, these measurements are processed by our PBench software, which manages both the control of the test bench and the organization of the cycles to be applied.
The cycle can be selected either by barcode or by datamatrix code on the injector, thus making the bench fully automatic.
As soon as the injector is positioned on its fork, the entire process is fully automated. This process includes clamping, pressurization, testing, and finally the unclamping of the injector.”
At the end of the test cycle, the injector is classified as good or bad based on the thresholds defined in advance for the measurements taken. The operator can then move the injector to the next step based on the result obtained.
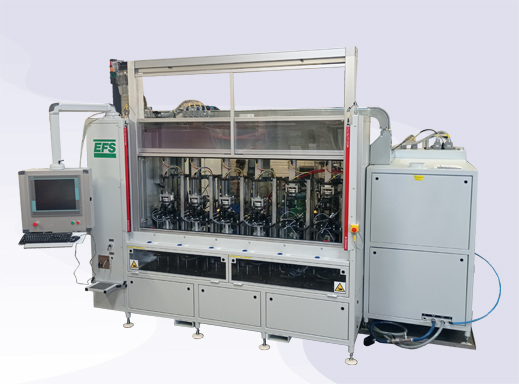
MEASUREMENTS TO QUALIFY THE INJECTOR IN PRODUCTION
- Validation of the injector flow rate for each pressure and pulse duration tested.
- Validation of the injector opening and closing delay for all its test points.
- Validation of its standard deviation in injected mass for each test point.
COMPACT
2400 x 1350 mm
AUTOMATIZED
Recognition of the cycle test with datamatrix code reading • Automatic clamping of the injector • Automatic test • Automatic unclamping of the injector • Database results saved after each injector tested with good or bad declaration for the piece under test
SCALABLE
Number of channel selectable from 1 to 6 • Selection of the flowmeter to use IFR or EMI3 • Motor power selectable depending of the high-pressure pump to use.
INJECTOR PRODUCTION TEST BENCH DESCRIPTION
- Instrumentation table including 1 to 6 EMI3 or IFR and manual injector tightening device
- Main high-pressure rail (500 cm³), but also 1 to 6 individual high-pressure rails (150 cm³).
- Oil station with main tank with test fluid temperature control system, lubrication tank, electric motor, high-pressure pump
- Electrical cabinet with various safety devices
- Pneumatic cabinet
- Measurement cabinet with EMI3 or IFR racks and bench supervision software (Pbench)
- Concentrator cabinet with database software (recipe creation, results display).
- Safety components (sensor, push button, emergency stop, switch).
- Air extraction vent
SEE OUR BROCHURE